Wireless charging can make drones fly farther
There are some large companies with ambitious plans to provide services based on drone fleets, and they are all eager to go beyond a major operational challenge: the flight time of commercial drones is limited by limited battery capacity. One way to solve this problem is a more efficient and flexible charging solution.
This also explains why people are so interested in WiBotic, which designs and manufactures battery charging solutions for drones and robots. The 4-year-old startup company recently received $5.7 million in Series A funding.
WiBotic provides wireless charging and power optimization solutions for the air, mobile, marine and industrial robotics markets. The company's adaptive matching technology provides a new method for inductive power transmission that can provide the power levels required by drones and other flying equipment.
This optimized solution provides detailed monitoring of battery charging parameters through a software library. Combined with the strategic deployment of wireless charging hardware, these software functions are designed to optimize the uptime of drones.
WiBotic wireless charging solutions also handle charging scheduling; they are designed to clear the way for multiple robots to charge from the same transmitter at different times.
Wireless Power Transmission (WPT)
The use of electromagnetic fields as a source of electricity can be traced back to the late 19th century, when Nikola Tesla demonstrated for the first time the transmission of electricity without wires. It is well known that wireless charging methods are a complex challenge in the design of transmitters, their location, maximum efficiency, and verification behavior of the entire system, requiring specific skills and the use of advanced tools such as numerical simulation.
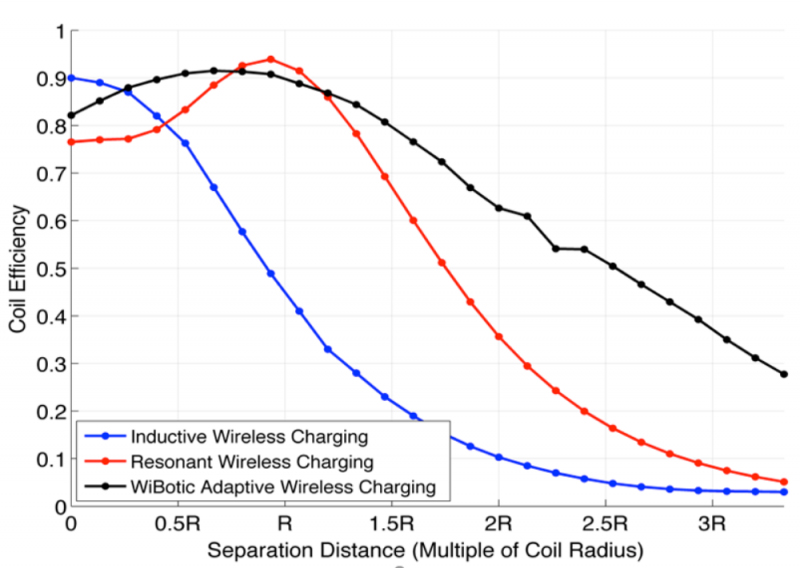
The most common method used in WPT systems is inductive coupling or MRI. Each method has advantages and disadvantages. The most common method is the inductance method-very common in consumer devices. Unfortunately, they are only effective when the antennas are very close. Robots and drones cannot be accurately positioned to ensure that the sensing system provides reliable charging.
Magnetic resonance technology is the latest technology and provides more flexible positioning. However, the typical resonance system has a special area where maximum efficiency can be developed. However, if the robot stops briefly or goes off-center, the efficiency will decrease and the number of recharges will increase.
WiBotic technology is based on the advantages of induction and resonance systems because it combines the advantages of both. Ben Waters, CEO of WiBotic, said: "Our patented adaptive matching system continuously monitors the relative position of the antenna, dynamically adjusts hardware and firmware parameters to maintain the highest efficiency-at high power levels, in vertical, horizontal and angular offsets. In the case of a few centimeters, reliable charging is provided."
Software algorithm
When the battery is low, knowing when to charge the drone is an important function for evaluating downtime. Different robots will have different types of battery chemistry, voltage and current. WiBotic's energy optimization software can evaluate the robots to be charged and determine the best charging method. Wibotic firmware allows the robot operator to monitor and set the required charging parameters. The onboard brain allows the drone to directly access the onboard charger to perform the same function. Structure The architecture of the wireless charging network allows the robots to stay charged, minimizes downtime, and reduces the total cost of the robot fleet.
Wibotic system architecture
The drone’s wireless charging station is a square platform (3 feet x 3 feet standard charging board), which consists of a "smart" sensor board. When the drone is landing, the sensor board determines the type of battery provided for the aircraft. Establish correct charging parameters. All WiBotic wireless charging systems consist of four main hardware components: transmitting unit, transmitting antenna coil, vehicle charging unit, and receiving antenna coil.
The transmitting unit generates a high-frequency wireless power signal through an AC power source. The signal is transmitted to the transmitting antenna coil through the SMA coaxial cable, where electric and magnetic fields are generated. The coil can be installed in any direction according to the runway of the drone.
Gallium nitride technology provides wireless automatic charging. These conditions require operation at high switching frequencies and maximum efficiency. In cooperation with GaN Systems, WiBotic integrates GaN equipment to provide the required power levels and antenna range requirements for drones and robots. In addition, the Vicor 48V VI chip PRM regulator PRM provides power to the transmitter on the WiBotic TR-110 wireless charging station, thereby providing wireless power to the robot/drone vehicle receiver. PRM accepts 48V AC and DC power supply and output voltage adaptive control and cuts off about 20 55V.
Through the wireless drone charging system, the entire charging process can be remotely monitored and controlled through cloud-based software, APIs and tools to ensure that the drone is charged as quickly as possible when needed, or when the flight plan is not huge Charge as slowly as possible.